HOME
Introduction
Design
Stands and Blocks
Shaping
Polystyrene
Epoxy
Glassing
Hot coat
Fins
Sanding
Art Work
Gloss Coat
Leash Plug
Books
Material Lists
Resin Amounts
Equipment List
Misconceptions
Tips
Sm Wave Design
Research
Videos
Helpful Links
This is your site. It is not biased
by any direct advertising and no money is accepted for any links shown.
It is made for you and supported by you.
PLEASE DONATE!
HALL OF FAME
~~~~~~~~~~~~~~~
Thanks to the users below
for keeping this site alive and unbiased with their donations.
Mark Sadler
Kevin Kuzma
Mark Griffith
Kirra Oredson
Logan Leitch
Joyce Shingler
Alex Bayer
Greg Bayer
Ian Pirsch
David Shell
Fab Ordonez
Tom Walczewski
Anthony Rynicke
Peter Young
Lori Hartline
Terence Harper
Robert Campbell
Thomas Gustafson
Michael Filanowski
John Gaudette
Philip Meagher
Russell Simms
Randall Kirkpatrick
Calvin Arnold
Preston Renbarger
Mark Schreiter
Mike Sheldrake
Ritchie Ginther
George Young
Michael Simbulan
Bradley Saviello
Poolguy Network
Elan Yaari
Mathieu Corbeil
Sergey Terentev
Anthony Azcona
Hamish Eassie
David Merga
Spencer Ward
.
|
POLYSTYRENE
I advise letting economics help you make your decisions as to which
materials to use. A good surfboard can be made with any of the materials
mentioned in this book. Allow me to simplify your decision by suggesting
the following:
1. If you live where you can economically drive to a polyurethane
foam distributor, (www.foamez.com, www.surfsource.net, www.fiberglasssupply.com
etc.) buy a roughly shaped polyurethane blank.
2. If you have to pay shipping for a polyurethane blank, consider
buying
a partially preshaped polystyrene blank (same companies as in #1
above, and, as in paragraphs below).
3. If you have to pay shipping for a partially preshaped polystyrene
blank, consider buying polystyrene block foam. The companion DVD
to this book (in the left column) shows how build a block foam board
from start to finish, including bending foam (bending saves even
more money).
You might save money by using polystyrene block and you might make
a lighter board, but you will require probably four
times more labor to shape polystyrene blocks, compared to a polyurethane
surfboard blank. Consider partially pre-shaped polystyrene blanks,
which are now widely available. Polystyrene surfboard blanks come
in the following two versions: 1. A rectangular shape,(no outline
or rails) with a stringer glued in, and the rocker planed in. 2.
The outline, rails and rocker molded in, and a stringer glued in.
Polyurethane blanks come with the outline, rails and rocker molded
in, and a stringer glued in. Note that the rectangular polystyrene
(more common) is about twice as hard to shape, compared to the molded
polystyrene and molded polyurethane.
When using polystyrene foam epoxy resin must be used to saturate
the fiberglass cloth (laminate layer) (most surfboards have 3 resin
layers; the laminate coat, hot coat, and gloss coat).
Epoxy resin is necessary because polyester resin has styrene in
it and will dissolve the styrene in polystyrene foam. Epoxy
resin is roughly twice as fracture resistant as polyester resin
(not twice as strong) and a little more than twice as expensive.
Consider that besides the extra labor, much of the money you saved
on polystyrene foam will be lost on the extra cost of the epoxy
(See EPOXY).
Finally, keep in mind that if you chose expanded polystyrene (EPS)
(beaded foam) and it gets fractured, it will absorb more water than
polyurethane foam or extruded polystyrene foam. It is very
important to dry it out and fix it immediately when damaged.
I recommend installing a screw out plug/vent like some sailboard
companies do, so any water can be easily dried and drained.
You usually will not be able to determine the grade but, if you
can, get the highest, least absorbent grade of expanded polystyrene
foam (beads more tightly fused). Most EPS blanks are 2lb/cu.ft. Blanks are available in 2.5 and 3lb. also - water absorbtion is unlikely to be a problem with these denser blanks. EPS is an especially good foam if you are willing to stop surfing
when it gets damaged. My experience is, for most surfers, water
absorption is not a big enough problem to cause them to decide against
using it again (especially with recent improvements in all EPS due
to a huge lawsuit). Polyurethane and extruded polystyrene
(see bottom of this page) are much less water absorbent in a fractured
shell.
For all of these reasons, I believe a polystyrene blank or block
is mostly worth considering for savings due to possible high shipping
costs of polyurethane blanks. Polystyrene foam is more widely available
than polyurethane foam. A polyurethane surfboard blank is usually
easier to shape (because it is already mostly shaped) and will generally
give you less problems later on, but high shipping costs should
make you consider polystyrene.
On the good side, polystyrene/epoxy boards tend to be more damage
resistant, lighter, and less expensive than polyurethane/polyester
boards. Most people are happy with their expanded or extruded polystyrene/epoxy
boards. One other benefit of block foam is the freedom to
make an unusual shape that would be impossible with a polyurethane
surfboard blank (such as a very wide, thick and, short board).
By using block foam, it is possible to reduce the total surfboard
material cost by about 25%. So, if you are determined to go
with polystyrene, here is what I suggest you do...
You can buy expanded polystyrene blanks which are partially shaped
with stringers from: www.surfsource.net, www.foamez.com, fiberglasssupply.com
and... Segway composites and Hydrofoam in California, Craig Chafin
and S - Foam in Texas, Coda Core and Davo in Florida, Natural Art
in Cape Hatteras, North Carolina, Fly in New Jersey, Shuller systems
in Seaside Oregon (I have only dealt with the first three companies,
and do not have any more information on the others). You can also
buy block foam from a local supplier (if possible). Most large
cities will have listings in the yellow pages under foam,or insulation.
Also, you can do a search on the internet. Type www.dogpile.com in the address bar. Type polystyrene foam and the name of
a large city near you in the search box. Also try www.thomasnet.com.
Please do not email me asking me to find polystyrene foam for you).
If you wanted an 8' board you might order one of the following;
1 - 8'1" x 24" x 6" block of 2lb./cubic foot
expanded polystyrene, or (if you are using a stringer, or glue joint) 2
- 8'1" x 12" x 6" blocks.
If you are using block foam I would like to encourage you to make
a stringerless board, or a board with an epoxy glue joint.
This will save labor, and will probably save weight and money.
If you intend to do without a stringer I recommend the following
layers of cloth: 4 oz. "E" cloth - 2 top,
2 bottom, and 2 deck patches. If doing without a stringer,
are over 160 lbs., or intend to ride hollow waves, or intend to
make a thin board, I highly recommend all 4oz. "S" cloth
layered as above. Another alternative is 4.8 oz. carbon fiber
cloth - 1 top, 1 bottom, and 1 deck patch (suitable carbon cloth
not available in 2008 - please email me if you find an economical
source).
Do not use foam from Lowe's, or Home Depot for your first board. These foam sheets are 1lb/cu.ft. Use at least 2lb/cu.ft. foam on your first board. Many builders have written me claiming poor results with 1lb foam. A good board can be made with this foam, but you will spend more on the extra shell material than you save on the foam - plus other negatives such as denting, and delaminating.
If you must use a stringer in your block foam, consider going to
Lowe's etc. and buying the cheapest 4'x8'x1/8" paneling.
This should be about $14. If your board will be over 8'5"
(an 8'5" stringer can be cut diagonally from 8' paneling)
it will be hard to find an inexpensive stringer. Consider
an epoxy glue joint,or epoxy with fiberglass cloth in place
of the stringer (it will be lighter yet similar in strength to a
1/12" stringer with hot glue etc. If you insist on a stringer,
do steps 1 - 5. If not using a stringer see step 6.
- Using your rocker template from the DESIGN chapter, mark the
outline of the stringer on the paneling etc.
- Cut slightly outside the lines so the stringer will be about
1/4" bigger than you want it when finished shaping.
- Trace the stringer outline on to the four blank edges as shown
in Fig. 13.
- Cut the stringer with a handsaw etc. and go over the edges
with a surform pocket plane etc.
- Rough the stringer on both sides with #50 paper etc.
This can be done with a 5" rubber backing disk on your drill.
- If not using a stringer, (recommended) mark the two edges of
a single blank (if possible) with the roofing felt rocker template
(mentioned above) as in Fig. 12. Take extra care to keep any epoxy
or glue away from any area to be shaped. If you are glueing sheets
together, stay at least 2” away from outside edges for face
to face gluing, and stay at least ½” away from top
and bottom edges for edge to edge gluing. If epoxy gets into the
area to be shaped, you will probably spend more time trying to
get this area even, than shaping the entire board. When substituting a glue joint for a stringer, use epoxy (epoxy is the strongest adhesive).
- If using a stringer, mark the outline of the stringer on the
four edges of the 2 foam blocks. Make sure they will all
line up exactly with each other (measure) when you glue in the
stringer as in Fig. 13.
Figure 12
Fligure13
- Use 6oz. total epoxy resin/hardener (see GLASSING and EPOXY).
Brush 3 oz. on each side. This will probably seem like too little
epoxy but resist using more or you will have serious problems
getting the stringer even with the foam.
- Sandwich the stringer between the foam blanks as in Figures
12 & 13. If you are not using a stringer try to keep
the epoxy about 1/2" inside the lines - this will make
it much easier to shape.
- After the epoxy hardens put the blank on the stands. It will
be a great help if you can have someone hold the blank steady.
If not put some weight on it (wrapped in a towel). Take your drill/disk
sander with #50 disk and start very lightly removing foam. Start
where the thickest areas of foam need to be removed. By the time
you get close to the black lines you will probably get the hang
of it. If you you are confident, try a #12 to 20 disk, or a power planer.
If you are gouging holes in the foam, give it up and do it all
with the, #12 or #16 block.
- Once you get everything down to the black lines, prepare to
mark your outline, and finish shaping, as mentioned
in DESIGN and SHAPING. Note: I recommend using scrap foam
to practice getting the feel of removing foam with a drill sander.
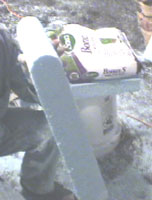
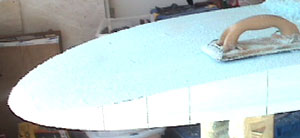
Alternative method:
- After the blank is glued, (if needed) mark the outline template
on the blank first (before the rocker template).
- Cut the outline as in SHAPING. With a sharpie pen, mark dots
(as you did when you made your rocker template) on the blank edge
corresponding to the amount of rocker at that point (nose tip,
3", 6", 9", 12", 18", 24"etc.) You
will need less points as you get further from the ends.
- Connect the dots using a 1/2" x 24"' piece of roofing felt
as a flexible straight edge. Note: Make this strip of roofing felt 1/2" on one end and 1/4" on the opposite end. Cut a line (tapering line) between the 1/2" and 1/4" measurements. Use the 1/4" end on the nose tip and 1/2" end towards the tail - this will tend to follow the measured nose rocker points without wrinkling, and will create a nice nose rocker even if no points are measured.
If measuring, any facets (angular rough spots) are easily sanded to curves.
This alternative method will save labor, but it makes it a little
harder to exactly copy an existing rocker.
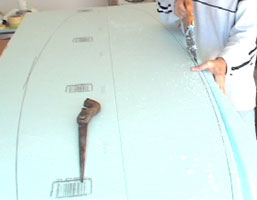
When you finish take interior/exterior lightweight spackling and
your squeegee (cheap plastic squeegee works well) and spread it thinly
over every inch of foam. Scrape off the excess with your squeegee
being careful not to scratch your blank. Sand it lightly with approximately
#120. Make sure it's completely covered (not scratched through)
or it may absorb a lot of expensive epoxy and become heavy. See
EPOXY. Spackling may not be needed if you have
the highest grade of polystyrene. This grade is less absorbent.
Use the spackling unless you are sure. Although I mention
spackling seal numerous times, do not use it for large repairs,
and never on extruded polystyrene. Note that the spackling does
not completely seal the blank - epoxy migrates through to the foam
at a reduced rate. Consider the sealer below.
Alternative sealer: For a stronger laminate with slightly more weight
try the following. Mix epoxy and hardener with microsphere thickening
agent to a mayonnaise thickness. Spread and sand as paragraph above.
One more alternative is to use 2lb./cubic foot (25psi - pounds
per square inch) extruded polystyrene foam (XPS) - Dow Square Edge,
or "blue board". Please try to keep and open mind,
and disregard much of the information you might have read online
etc., about this foam. The delamination problems which have caused
some builders to stop using this foam can be solved by following
the directions below. A very good board can be made with this foam
if you will simply build the board a little differently. This foam
does not have the water absorption problem that expanded polystyrene
has. Extruded polystyrene is stronger (pound for pound)
than polyurethane, or expanded polystyrene (most surfboard polyurethane
is about 3lb/cu.ft.). If you build with this foam using
conventional methods, you are much more likely to have delamination
problems.
Please allow me to insist you do the following:
- Use an epoxy glue joint/s (in place of a stringer/s) - one
is o.k., two is better.
- Finish the blank by sanding lightly with #20, leaving hundreds
scratches and small pits.
- Add about 5% more resin to the laminate after dragging the
excess resin out of the cloth.
The extra resin will fill in all the pits and scratches left on
the rough blank. I realize it is hard to scratch and tear
the foam of a blank you worked so hard to perfect, but do not skip
this step. The pits and scratches greatly increase the bond,
and with the glue joint/s, will minimize the delamination problem
to a level equal to other foams. As with all boards, but especially
XPS, avoid exposing an XPS board to a car interior on a hot day
with the windows rolled up. This foam is available in sheets
8' x 4' x 3" and 8' x 2' x 4" thickness maximum,
so you may have to glue (epoxy) two sheets together. It is
possible to make two good boards out of one 8' x 4' x 3" sheet,
if you bend the foam as in the paragraph below. XPS was available
in 2006 for $46 for a 8'x4'x3" sheet.
Bending foam using one of the following methods will save money
and labor - by allowing you to use a thinner blank which will
require less foam to remove. This method can be used with
any stringerless foam (you will be able to bend an epoxy glue joint,
but only about 2"). Align the rocker template nose tip
with the blank nose tip and mark as much of the nose rocker curvature
that the blank thickness will allow. Mark about half the tail rocker
(the tail will bend about an inch when you bend the nose).
Shape the rocker (as much as possible), cut the outline, and completely
finish shaping the blank as mentioned previously.
You can increase the nose rocker on any stringerless blank by using
the following method:
- Move the nose side rack toward the center of the blank before
you laminate (the blank will sag about 1/2" - 1 1/2").
- Cut off all but the threads of the largest plastic sheet rock
anchors (about 3/8"diameter). Screw the anchors into
the down (dry) side of your blank. (nose and tail - if you
do not weight the tail the blank will tip off the racks).
- Insert a screw in the anchor, tie one end of the string to
the screw, and the other end to a weight (brick etc).
- If your nose tip is too thin to use plastic anchors you can
cut a 1'' slit in the mid tip of the blank nose.
- Cut a 1" slit in the cloth that will cover this area.
- Cut off about 2" of a mixing paddle, tape wax paper to
it, and drill a small (about 1/8") hole in the middle.
- Tie a 1" broken pencil on top of the mixing paddle to
keep the cord from pulling through the hole.
- Attach a weight to the other end of the cord.
- After the cloth is saturated, slide the cord through the slit
with the cut paddle sitting on top of the wet cloth, and the weight
hanging slightly towards the tail down in a bucket ( to keep the
weight from swinging forward, which will cause the cord to pull
out of the slit).
When the lamination hardens it will permanently hold the bend (it
will spring back about 1/4" -1/2"). You can change
the amount of curve in different areas of the blank by moving the
racks, changing the position of the weights, and the amount of the
weights. This can all be checked (before cloth saturation)
by putting weights on top of the blank. Try not to bend the
foam more than 3". Note: leave plastic anchors in the blank.
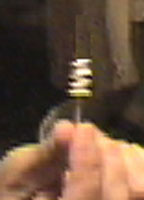
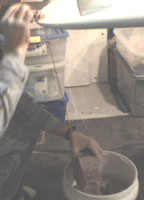
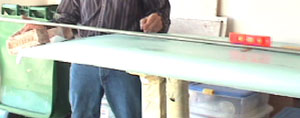
You can bend the foam to match a pre-rockered stringer, then clamp,
or weight it together. This is what Clark Foam did.
I no longer use stringers (too expensive, too heavy, and too much
work). It is more effective to use heavier cloth instead of
stringers - the board will be more damage resistant.
To make a board that is almost impossible to dent or delaminate,
consider the following: Puncture or drill the blank every 2"
(bottom to top) with 1/8" drill bit or 1/8" steel rods.
Make a puncture tool by first drilling 1/8” holes in a 6”x
6”x 5/8” piece of wood. Insert 1/8”x 3 - 4”
steel rods (9 rods) into holes in wood, and epoxy in place. The
holes in the foam will fill with resin when laminating, bridging
the top and bottom together (do this only with uscomposites Klear Kote Epoxy, as it is much thicker than most other resins).. On the first lamination, wipe the resin,
which will drip out the opposite side of the holes, when it gels. Also; 3/16" holes can be filled with 3/16" bamboo barbeque skewers, available at most grocery stores - this method will work with any resin (see TIPS chapter, DELAMINATIONS section).
This has been tested since 2005. Please do not do this in order
to reduce cloth amounts.
If you glue sheets together try to figure out where the glue joint
crosses the outline and rocker of your board and avoid putting glue
there (otherwise it will be much harder to shape at the glue joint).
Yes, a good surfboard can be made with extruded polystyrene foam. www.pointblanks.com is making virtually unbreakable surfboards using extruded polystyrene.
They do not sell foam. On extruded foam, do not use lightweight
spackling, or any art work. It tends to delaminate at these
areas. Repairs can be done by one of the two following methods:
- Cut a foam block, cutting the damaged area to match the block.
Epoxy the block in place (epoxy only on the bottom of the block).
Shape to fit.
- Mix fine foam dust with barely enough epoxy to hold it together.
Fill, and sand.
This is my favorite foam but it is a lot of trouble. Build
with it only if you are willing to use the unconventional methods
mentioned four paragraphs above. We find XPS is especially
good for situations where the board is fractured, due to rocks etc.,
and the rider refuses to fix it immediately, or ever (for practical
purposes, it is impervious to water).
I like extruded polystyrene but, it may not be worth the extra
effort. Expanded polystyrene is easier to find, can be bought in
nearly any thickness and length (blocks), is better suited to a
stringerless blank, and is sold in partially pre-shaped blanks.
Remember, you can buy polystyrene block (EPS or XPS) in one solid
sheet, at the minimum thickness of your board, bend it after shaping,
and save about 75% of the cost, of a pre-shaped blank (this is the
cheapest and hardest way to make your own blank).
Another alternative is to strip the fiberglass from an old board.
This can be done by running a 3" abrasive disk around the circumference
of the mid rail, cutting barely through the fiberglass into the
foam. Carefully pry the fiberglass off the rails (you may
have to make extra cuts where the curves are small - perpendicular
to the mid rail cut). Once the rails are striped the fiberglass
will pull off the remainder of the board very easily. Re-shape
the blank
Some people are using 2 lb./cu. ft. polyurethane block foam
to build surfboards. My friends and I have tried it numerous
times. We are sure you will like 2lb/cu.ft. polystyrene block
foam better. It is stronger and less expensive. 2lb
extruded polystyrene is 25psi. This foam is also available
in 40, 60, 80, and 100psi. Although the tendency to use lighter
foams and thicker laminates is now more prevalent, I believe there
is good reason to experiment with the higher psi foam. The
60psi foam is only 3lb/cu.ft (this is about twice as strong as standard
polyurethane surfboard foam of the same weight). Those who
have tried the 40 and 60psi foam claim this will allow a builder
to reduce the cloth approximately by half and have a stronger, and/or
lighter stringerless board. This is unlikely to save
money - the extra cost of the foam is more than the savings in cloth.
and, you will not be able to bend 40 or 60 psi foam. Please
use the 2lb. type for your first block foam board.
Please resist the temptation to use sheets of foam from Lowes or
Home Depot. Many builders have tried it and many of them have emailed
me with the following problems: denting, delamination, water absorption,
and shaping difficulties at the numerous glue joints.
Some suppliers of partially preshaped EPS blanks are now offering
a choice of foam densities. You will have a more durable board
(other things being equal) if you choose the higher density foam
(2.5 lb./cu.ft. & 3 lb./cu.ft.). There is a reason Clark
Foam sold 3 lb. and 3 lb.+ blanks. It is often more cost effective
to use a higher density core and a lighter shell - the foam is usually
less expensive than the cloth and resin.
I added this paragraph due to many emails. You can ruin your blank
in a split second with a hotwire cutter (I have). For a the building
of personal boards I advise extra caution when using a hotwire cutter, or a planner.
An inexpensive drill with a sanding disk is very efficient at removing
foam. If you are committed to shaping numerous polystyrene
blanks (working for profit) you might consider making a hot wire
cutter to cut the excess foam down to the stringer line etc.(please
do not make a hotwire cutter for one board). Also you could buy
a planner modified for foam (Hitachi from www.foamez.com - these
are outrageously expensive now). If you buy a non modified
planner (sometimes ten times cheaper), look for one with a 3/16"
cut (check Harbor Freight). Note that you can make the planner cut deeper if you
sand/grind the aluminum front plate down (this is what they do when
you buy a modified one). Remember: A planner is not essestial for shaping a surfboard. A drill sander
and hand blocks will suffice. If you use a hot
wire, please practice on scrap pieces, please wear a respirator,
and please set it up so power can be disconnected quickly. After weeks of design and testing the author made a video on youtube featuring three simple, practical hot wire cutters. The you tube link is below:
https://www.youtube.com/watch?v=juYzB7fF-DQ
Please do not try to make your own foam blank from liquid chemicals.
I have tried it numerous times and found the results non useable,
for practical purposes, in a garage setting. If anyone figures
out how to do it economically, and reliably, please email steve@surfersteve.com
Allow me to simplify your decision by suggesting the following
1. If you live where you can economically drive to a polyurethane
surfboard blank distributor, (www.foamez.com, www.surfsource.net,
www.fiberglasssupply.com etc.) buy a roughly pre-shaped polyurethane
blank.
2. If you have to pay shipping for a polyurethane blank, consider
buying
a partially preshaped polystyrene blank (same companies as in #1
above, and, as in paragraphs above).
3. If you have to pay shipping for a partially preshaped polystyrene
blank, consider buying polystyrene block foam. The companion DVD
to this book (in the left column) shows how to build a board of
block foam from start to finish, including bending foam (bending
saves even more money).
Most first timers get through the shaping ok, if they follow the
directions. Many people claim glassing is harder.
[Next]
|
|
|